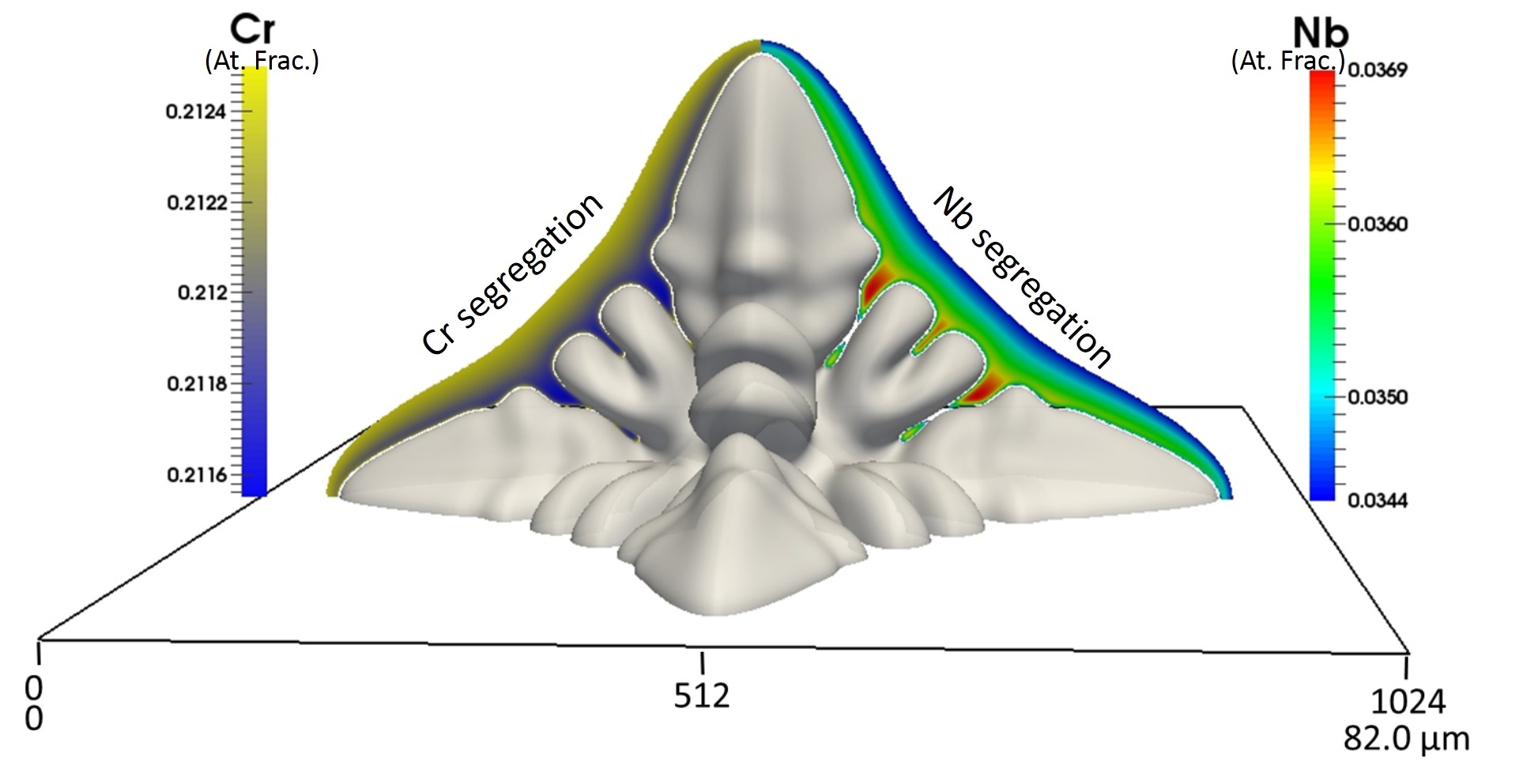
ICME (Integrated Computational Materials Engineering) Lab
ICME is defined as “the integration of personnel (e.g., engineers, designers, etc.), computational models, experiments, design, and manufacturing processes across the product development cycle, for the purpose of accelerating and reducing the cost of development of a materials system or manufacturing process”
This approach uses computer aided techniques to link materials science, product development and manufacturing processes to create the best component for a specific application and accelerate product development, thereby reducing the cost of manufacturing. Simulations in materials science aims at mimicking and/or reproducing an experiment based on the theory behind it. The simulations used in Metallurgical and Materials Engineering discipline cover a wide range of length scales. The word ‘Integrated’ in ICME illustrates the integration of material models at various length scales (from electronic scale to macro scale) to ‘Engineer’ industrially relevant products. It focuses on the process-structure-property-performance relationship in materials and helps in evaluating the properties of materials at a given scale by using models or information from other length scales. Hence, multiscale modeling is imperative in an ICME setup as a part of what’s commonly referred to as ‘vertical integration aspect of ICME’. ICME adds to this, ‘horizontal integration’ to integrate multiscale modeling across the process chain. ICME plays a key role in modeling and simulation of the microstructure evolution, development of suitable material models, prediction of life of components during creep, fatigue and radiation damage and optimization of processing parameters to increase the quality during manufacturing.
The ICME Laboratory at the Department of Metallurgical and Materials Engineering, IIT Madras is an environment hosting members from different research groups in the area of Computational Materials Engineering. The objective is to create a collaborative environment where the students learn from each other and thereby progress faster. This lab has a wide range of software and hardware resources available. Apart from commercial software such as Abaqus, Ansys-Fluent, MATLAB, Mathematica and Comsol that are being maintained by the Institute, ICME lab has access to software such as Thermo-Calc (including Dictra and TC Prisma), Micress (including Homat), JmatPro, Pandat, FactSage, MatCalc, Simufact-Forming, Simufact-Additive, Simufact-Welding, MedeA, HSC Chemistry, VASP, PyroSim and WIEN2K. There are also some open source software such as OpenFOAM, LAMMPS, ParaView, OVITO, AtomEye and Dream3D which are being used in the lab. When it comes to hardware resources, apart from the Desktops and Workstations located in ICME lab, there are six high capacity rack mountable workstations located in the P. G. Senapathy Computer Centre, IIT Madras. These machines run 24x7 without common power failures and the students use these machines to carry out heavy computational tasks. The major areas of focus in the ICME Lab are Phase Field Simulations, Computational Thermodynamics, Computational Fluid Dynamics, Crystal Plasticity, First Principles Calculations and Finite Element Analysis.
Prof. K C Hari Kumar’s group mainly works on the development of phase diagrams using the Calphad (Calculation of Phase Diagrams) method coupled with ab initio calculations. The vital experimental information required for modelling, such as, thermochemical (like enthalpy, entropy, Gibbs energy etc.) and constitutional (like phase boundaries and invariant reaction coordinates) data are obtained from literature and critically assessed. The missing thermochemical data is obtained using ab initio calculations at 0 K. The thermodynamic properties above 0 K are also estimated using certain approximations. The theoretical and experimental data are combined to model the Gibbs energy parameters for different phases in a system using statistical techniques. Thermo-Calc is the main tool used for thermodynamic modelling to obtain the model parameters. Pandat software is also used for calculating the phase equilibria. For ab initio calculations VASP, PHONON, Phonopy and ATAT codes are extensively used. In addition to this, precipitation simulations are also carried out in this group using softwares such as DICTRA and MatCalc.
Prof. Gandham Phanikumar’s group performs simulations at different length scales and bridges them. Phase-field simulations are used for microstructure evolution in metallurgical processes, which takes data from CALPHAD databases and molecular dynamics (LAMMPS). The group has developed a phase-field code for solidification. At macro scale, ‘Finite Element Method’ and ‘Control Volume Method’ are used to model various industrial processes like welding, cladding, solidification and metal forming. The mathematical technique of ‘Homogenization’ is used to stitch the micro- and macro-scale simulations. Software tools such as Micress, Homat, Simufact, Sysweld, OpenPhase, OpenFOAM and Abaqus are being used for microstructure-property correlation. Knowledge representation using semantic web technologies is an important element of ICME approach. Thanks to the free Java-based tool “Protege” from Stanford, one can start creating ontologies of their domain knowledge with all the necessary tools for authoring, reasoning and visualization in one package. The group is collaborating with Prof. N.S. Narayanaswamy (CSE, IITM) on creating ontologies for materials domain. This is perhaps the first group in materials domain in our country to be working on ontologies. In order to accelerate the simulations, parallel programming techniques are being implemented using OpenMP, MPI and OpenCL. Dasari Mohan, a PhD student in the group, has developed an OpenCL version of his phase field code that has clocked 2 teraflops on AMD FirePro W8100 card.
The research activities of the group lead by Dr. Anand Kanjarla aims at understanding the mechanical behaviour of materials from a microstructural/crystal plasticity point of view by developing constitutive models, running simulations and performing experiments. Most of the efforts are focused on the mesoscale or the length scale of a microstructure and linking it with engineering or macro scale. This is done by writing in-house codes capable of predicting both average and local stress strain responses, creep, texture evolution and mechanical anisotropy in a wide range of materials such as nickel based superalloys, titanium alloys, magnesium alloys, duplex stainless steels and irradiated materials. The group has expertise in solving elasto-plastic boundary value problems by spectral methods using Fast Fourier Transforms (FFT) and writing crystal plasticity User Material (UMAT) subroutines that can be used in commercial Finite Element packages such as Abaqus™. On the experimental side, mechanical tests performed using regular UTMs and thermomechanical simulator Gleeble™ coupled with detailed characterization techniques like EBSD, XRD, TEM, etc., are routinely used both to validate the models and gain fresh insights into mechanical behaviour.
Dr. Sabita Sarkar’s group works on the fundamental understanding of transport phenomena in multiphase systems such as gas-particle, gas-liquid and gas-liquid-particle system in the interests of metallurgical processes. They develop mathematical models based on mass, energy and momentum balance to design and optimize a process reactor. Commercial software like Ansys Fluent, Ansys CFX and in-house codes are used to solve mathematical models. Often, these mathematical models are validated with lab scale physical model experiments. Current research interests of this group include development of dry slag granulation process reactor for energy recovery from blast furnace slag, fluidized bed gas solid reduction reactor, modeling of secondary steelmaking processes such as degassing, molten steel - slag - gas interactions and hydrodynamics in steelmaking ladle, hydrodynamic modelling of tundish etc.
Dr. Ajay Kumar Shukla‘s group works on the modelling and simulation of the various ironmaking, steelmaking and their allied processes. Some of the projects the group works on are application of computational thermodynamics using FactSage for mathematical modelling of RH degassing process of Steelmaking, use of MATLAB for transport phenomena based model of blast furnaces and COREX iron making process, use of MATLAB and METSIM for static and dynamic modelling the BOF steelmaking process and control and optimization using Artificial Neural Network and Genetic algorithm (ANN & GA) methods, use of ANSYS Fluent for simulating the solidification modelling of twin roll casting process, physical modelling of dry slag granulation process of blast furnace slag for producing clinker compatible product, and development of mathematical model for heat recovery system.
Dr. Sreeram Kalpathy’s research group mainly focuses on modeling and simulation of interfacial phenomena in soft matter like Polymers and Colloids. Interfacial phenomena such as the hydrodynamic stability of free and bounded thin liquid films in the presence of surfactants are modeled using lubrication Theory. Linear stability analysis as a tool is used to get insights about the fastest growing perturbation wavenumbers. This comes as a valuable asset to coating and printing processes, in identifying the parameter that can be tuned to achieve the desired length scales for patterning and templating. Similarly, modeling of coating processes such as dip coating can also be a very good value addition to the coating process itself, for identifying the right experimental parameters to achieve a given film thickness. Software like MATLAB, COMSOL Multiphysics®, and self-written programs on Fortran F90 are being used to model the above-mentioned problems. Dr. Murugaiyan Amirthalingam’s research interests include additive manufacturing, welding processes development and modeling, steel products development and welding metallurgy. His students work on projects such as additive manufacturing of self-healing materials, hot forming of advanced high strength steels, hydrogen interaction and embrittlement in multi-phase Fe-C alloys, welding behaviour of automotive steels, CMT welding of aluminium alloys, and modeling elemental segregation during welding. Software used by the group include ThermoCalc, JMatPro, COMSOL Multiphysics, MICRESS, Sysweld, ABAQUS, Marc-mentat, Dictra, ImageJ, Simufact, Pandat and user developed codes to calculate distortion, thermal profile, phase field model in Fortran. Dr. Satyesh Yadav’s group works on First-Principles electronic structure modeling of the physics and chemistry of materials. Electronic structure modeling is combined with Elasticity theory, Monte Carlo methods and Classical and Statistical thermodynamics, to get a comprehensive understanding of the processing-structure-properties-performance relation in materials. The group mainly focuses on electronic modeling of materials for energy conversion, storage and optoelectronic devices. In addition to this, in order to capture phenomenon at larger length and time scales, atomic structure modeling of materials is
The ICME Lab is located in Room No 108, ground floor of the Mechanical Sciences Block (MSB). For more details, visit the ICME lab website: https://mme.iitm.ac.in/icme
References [1] Integrated Computational Materials Engineering (ICME): Implementing ICME in the Aerospace, Automotive and Maritime Industries. A Study organised by TMS. 2013.